In die casting process, using
mold release agent is universal to separate a part correctly. Therefore, release agent is indispensible.
furthermore, it is a very important part in die
casting process to select high-performance release agent developed by an optimized design for the following conditions to improve the quality of castings and maximize casting efficiency.
HJS has throughout analyzed and applied particular variables, which can take place in casting conditions, in many kinds to developing products. Thanks to that, we have succeeded in developing very advanced release agent ALUB¢ç series, which not only increase the lifespan of a mold longer than existing products, but also cast more parts in a shorter time.
The combination of engineer's expertise and high-performance release agent creates a very great synergic effect.
- eco-friendliness
- shortening of cycle time
- accumulation of mold and minimization of contamination
- fine exterior gloss
- optimization of diffusion time of release agent in a mold
- high mold adhesion test at a variety of temperature.
- maximization of inner quality of a casting: minimization of air bubble error
- stable releasing in unfavorable conditions: e.g. re-use or recycle
Corrosion Resistance Test
[ALUB¢ç (top left) release agent and comparison with 8 competing products]
Drop each of undiluted solutions (100%) of the competing products on a heated steel plate and compare corrosion resistance after 24 hours passes. Corrosion can take place not only in a mold, but also a cast product. Even with bare-eye inspection alone, it was confirmed that the corrosion resistance of ALUB¢ç release agent was much better than its competitors.
ALUB¢ç release agent |
Other companies release agent |
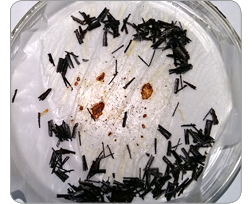 |
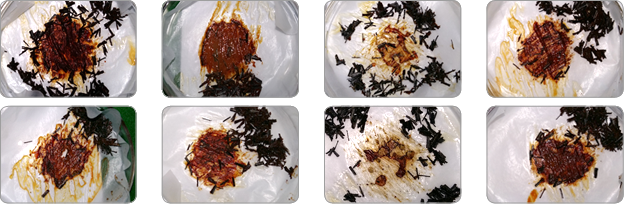 |
ALUB¢ç Release Agent: Mold Adhesion Test, Compared with Competitors
[Comparison of castings applied by ALUB¢ç release agent (left) and competitors (right)]
The picture above is one taken to compare the appearance of castings applied by ALUB¢ç release agent and competitors about a month after field comparison test.
ALUB¢ç product, which has more optimized defusion time, higher mold adhesion, and better releasing property than competitors in the same cycle time, minimizes the occurrence of fusion on the surface of the product right after casting.
In addition, a test was carried out with cast parts, which was applied with ALUB¢ç release agent and had not been in use for long after that. It was found that the casting applied with ALUB¢ç release agent didn't show change in coloring (into black).
For more information or consulting about die casting, please feel free to contact us.
We are ready to give you sincere response.
¢Ã INQUIRY